Aujourd’hui 90 % des gants en nitrile proviennent de Malaisie. Des équipements fabriqués dans des conditions de travail très dures (lire l’article du Monde diplomatique sur le sujet). Le tout sans aucune maîtrise de la « supply chain » : souvenons-nous de la foire d’empoigne pour obtenir des livraisons pendant la crise Covid.
Sécuriser l’approvisionnement d’un EPI critique
Pour changer la donne et sécuriser l’approvisionnement de cet EPI, les pouvoirs publics ont demandé au Resah, dans le cadre du consortium Re-Uni, de monter un marché inédit, avec des exigences strictes en matière d’implantation géographique, de qualité, de capacité de production en fonction de l’évolution de la demande, de stocks de sécurité déportés et de développement durable.
Attribué au groupement constitué de ManiKHeir (groupe Medicom) pour la partie fabrication, et de Didactic pour la facette distribution, cet appel d’offres, unique en son genre (achat d’1,5 milliard de gants d’ici au 31 décembre 2027), a favorisé la création d’une usine sise à Bessé-sur-Braye, à la frontière entre la Sarthe et le Loir-et-Cher. Un site qui sonne le retour d’un savoir-faire disparu dans l’hexagone depuis plusieurs décennies. Et qui permettra de créer localement environ 200 emplois.
80 millions d’investissements pour une usine modèle

© JM Delage
Sur place, la technologie déployée a impressionné une première délégation d’établissements invitée le 18 octobre à découvrir les lieux. Car la fabrication de gants d’examen nécessite une ingénierie pointue et une machinerie ultra complexe qu’on a du mal à imaginer. A terme, l’usine pourra compter sur quatre lignes de fabrication, d’une longueur chacune de 1350 mètres. L’une d’elle a déjà commencé à produire. Elle est entièrement automatisée, de la réception des matières premières jusqu’à l’emballage des produits finis. Aucun gant n’est manipulé par un opérateur.
Tout au long de la chaîne, c’est un véritable ballet qu’exécutent 25 000 « formes », moules reproduisant la forme d’une main. A la queue leu leu, elles descendent et remontent, tournent sur elles-mêmes au rythme des étapes du processus : nettoyage, trempage dans différents bacs de solution, rinçage, séchage, vulcanisation, démoulage des gants obtenus…
Une qualité supérieure et responsable
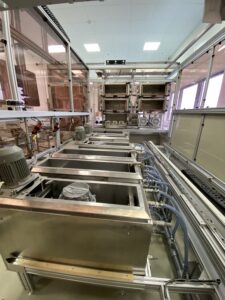
Au laboratoire, un robot teste les possibilités d’amélioration de la chaîne de fabrication © JM Delage
Pour se démarquer de la production asiatique, le suivi de la qualité à toutes les étapes est un leitmotiv. « Il s’agit de mettre en avant l’excellence française » a insisté Gérald Heuliez, DG de ManiKHeir. Pour parvenir à ses fins, l’entreprise a, entre autres, misé sur l’innovation. Disséminés, 1600 capteurs picorent des données toutes les 10 secondes. Une « control room », digne de la NASA, surveille la chaîne comme le lait sur le feu. Au laboratoire, un robot reproduit, avec des ingrédients similaires, le travail de la chaîne, histoire de vérifier que les performances attendues sont au rendez-vous. Le système met également au banc d’essai des pistes envisagées afin d’améliorer constamment les équipements.
Autre singularité par rapport aux gants fabriqués à l’autre bout du monde : la volonté de respecter au maximum non seulement la santé des utilisateurs, mais aussi celle de la planète. Une formulation sans chlore, ni accélérateur chimique, amenuise les risques d’allergies et de réactions cutanées. L’usine cherche à limiter son empreinte carbone et les impacts sur les ressources naturelles. De la conception à la livraison du produit fini, la production française permet de baisser de 30 % les émissions CO2 liées à l’achat de gants par rapport à un approvisionnement d’origine asiatique.

Des gants soumis à rude épreuve © JM Delage
L’exemple de l’eau est symptomatique. Car fabriquer un gant en nécessite beaucoup. Le site utilise 90 mètres cubes à l’heure, pompés dans une rivière toute proche. Mais il n’en consomme en réalité que 5 %. Le reste est recyclé ou rendu au milieu naturel après épuration. Une eau rejetée plus propre que celle prélevée en amont, assurent les dirigeants de l’usine.
Appel à l’adhésion massive
Commercialisés sous la marque Kolmi, les gants seront livrés à partir du mois de mars prochain. Acheter cette qualité responsable a évidemment un prix. Bien décidés à booster l’achat souverain, les pouvoirs publics assument totalement le surcoût. L’Etat prendra en charge le différentiel, calculé par rapport à un prix bas de référence. Pour mobiliser les hôpitaux, le ministère de la Santé a déjà publié deux instructions. Une troisième est dans les tuyaux.

Dominique Legouge, Gerald Heuliez, Sylvain Groseil, président du Resah, et Raphael Ruano, réunis lors de la visite de l’usine © JMB
Responsable du programme Phare, Raphaël Ruano, présent à la visite, a exhorté les hôpitaux à utiliser le marché. « Il faut que l’adhésion soit massive dès le début ». En effet, plus les établissements s’engageront, plus le système de tarif dégressif, déclenché par palier, fonctionnera. La DGOS recommande ainsi de ne pas activer les tranches annuelles des contrats en cours.
De son côté, Dominique Legouge, qui s’était également déplacé, s’est réjoui que le Resah « soit porteur de ce premier projet national de relocalisation industrielle dans le domaine des produits de santé qui ouvre la voie vers plus de souveraineté sanitaire et qui s’inscrit pleinement dans la dynamique hospitalière actuelle d’une plus grande responsabilité environnementale, sociale et économique par les achats. »